Moab, Utah is known for its phenomenal sandstone formations and vast open space for outdoor activities. The clients came to us with this site set amidst the beauty of the desert landscape surrounded by panoramic views. When we first visited the site we were awestruck by the beauty and grandeur of the red rock cliffs, valleys, and canyons that create a stunning and magnificent setting to behold.
There are certain projects where the relationship to the site is essential and this project was certainly one of them. The 2,000 sq. ft. home is simple in function and form with an asymmetrical gable roof volume that is extruded along the main axis of the house to form an exterior shroud that protects the interior spaces from the harsh desert climate. The orientation of the house on the site aligns with the sun’s path. The long axis of the house is focused to the east toward the point where the sun rises over the La Sal Mountains and to the west where the sun sets over the southern Utah cliffs. The common living, cooking and dining space of the house is located within this volume, allowing occupants to experience the sunlight as it moves through the space throughout the day.

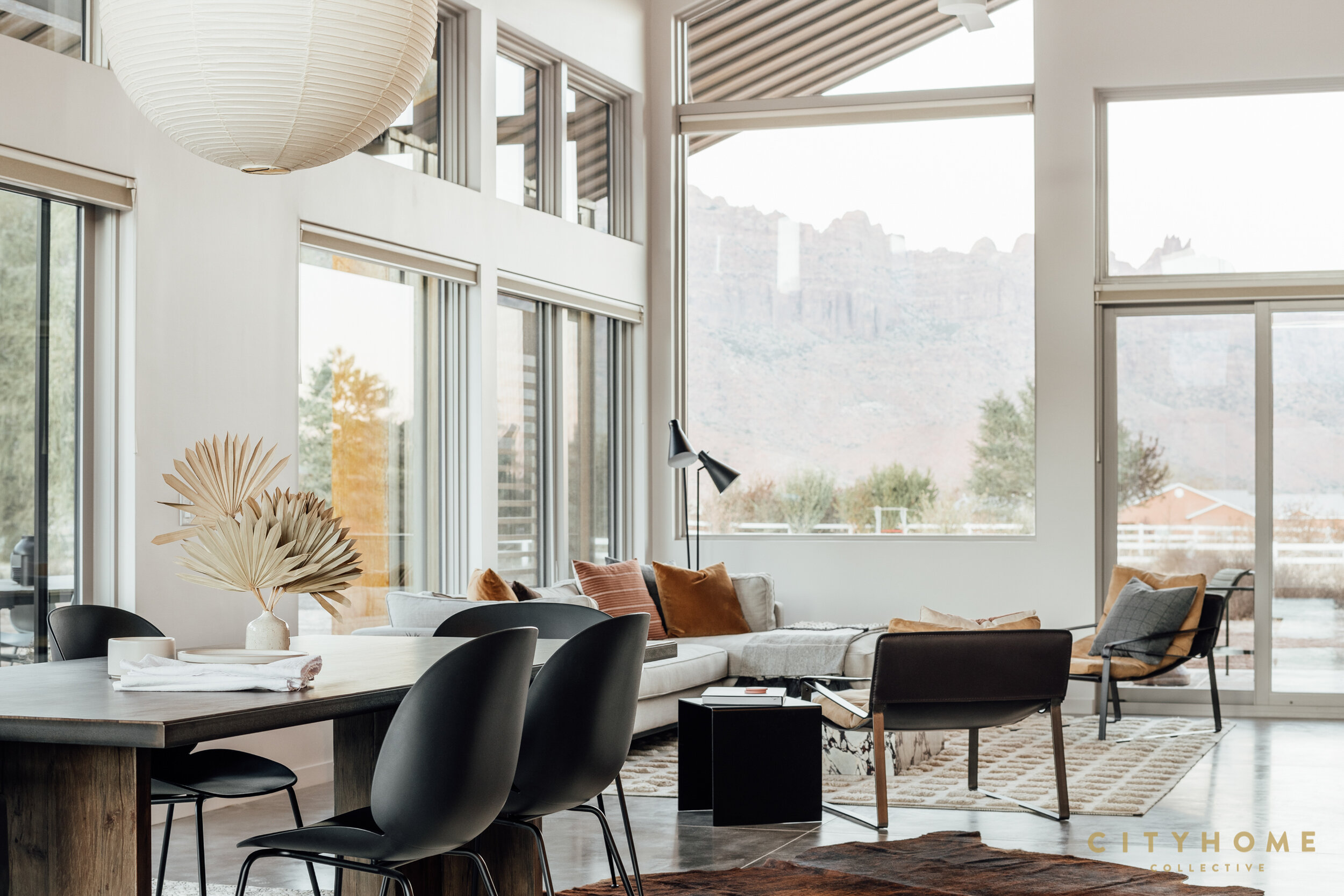
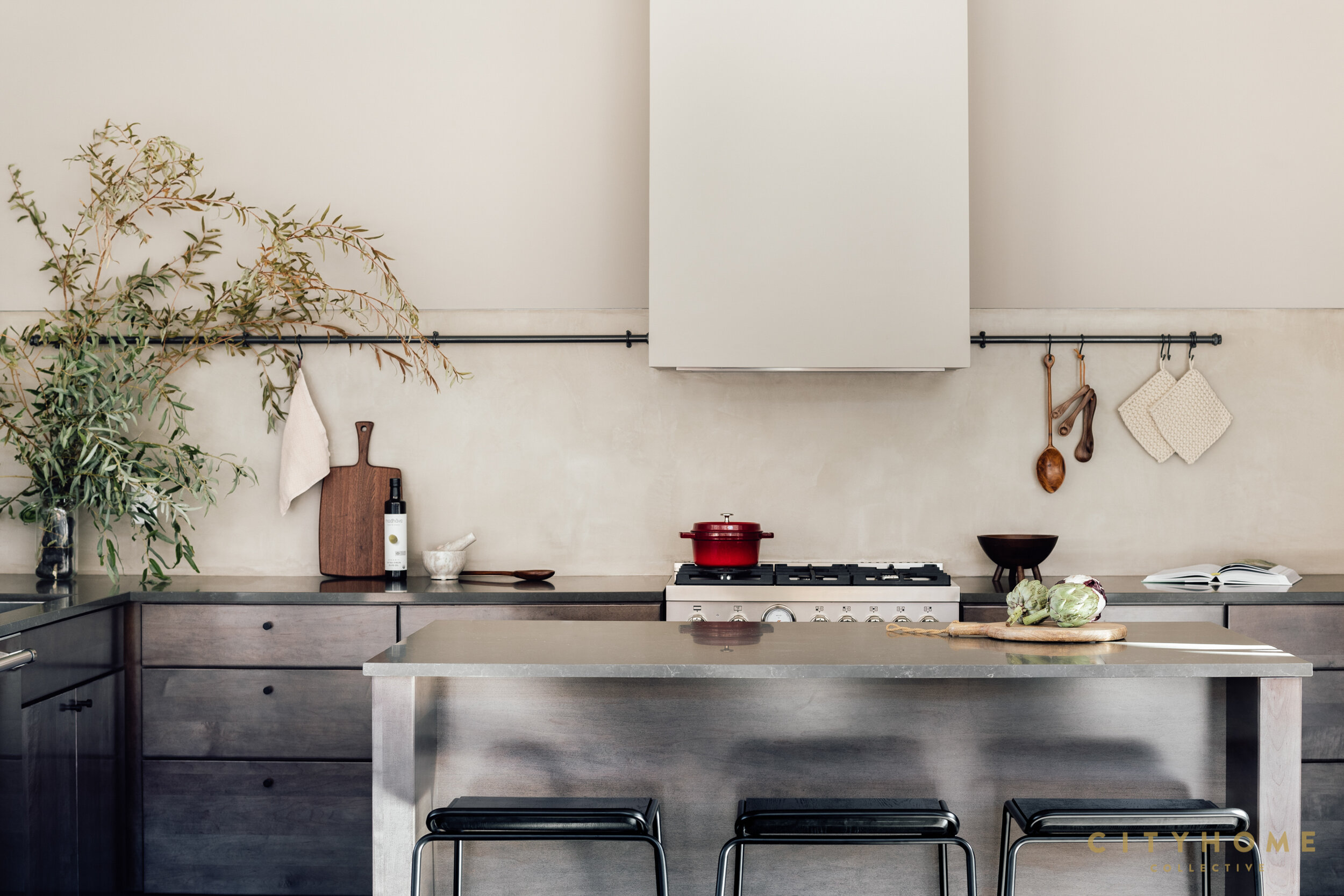
The material selected as cladding for the large exterior extruded roof form is a natural steel panel that is allowed to rust on the surface, creating a patina and pattern that references the red-orange sandstone cliffs. Weathered wood boards are placed around the doors and windows providing a similar but softer texture in the areas where one enters the house. The concrete floor slab is continuous from the interior to the exterior to reinforce the sense of continuity from inside to outside.
The southern wall, punctuated with a series of glass doors and windows designed to provide a connection to the landscape and panoramic views, is set in under the deep overhang of the roof to deliver shade in the hottest months. There is a hidden loft set at the top of the volume accessed by a simple ladder that offers an ideal space for reading and reflection. The bedrooms and bathrooms are all aligned along the lower north side of the house that has smaller horizontal windows to create view portals while retaining a sense of intimacy and privacy.
Sustainable strategies played an important role in the design of the house. Studio Upwall collaborated with Eco Logic Design-Build who specializes in high-performance construction. They were able to minimize the environmental impact of the house by using structurally insulated panel construction, energy recovery ventilation, radiant floor heating, etc.
The garage building, designed as a similar volume as the main house was clad in the same patina steel panels.
Photos and Interior design by: City Home Collective